在汽车、船舶等制造业研发体系中,AutoCAD等设计软件的采购成本长期陷入“预算黑洞”——某车企年采购费用超2000万元,但部门闲置许可证占比高达32%,同时核心项目却频繁遭遇“许可证饥饿”。其本质是需求与供给的断裂:粗放式的“按部门分配”模式,使软件资源沦为部门博弈的筹码,而非驱动研发的生产要素。破解之道在于构建数据驱动的需求分析模型,将采购决策从经验猜测升级为精准量化,实现“需求可测量、资源可调度、成本可优化”的三角闭环。
【深度解构预算失控的底层逻辑】
1. 需求黑洞:非理性采购的三大诱因
- 部门本位主义:设计部为争夺资源虚报30%需求,工艺部实际使用率不足40%
- 项目波动陷阱:船厂分段设计阶段许可证需求陡增300%,非高峰期资源闲置
- 版本迭代盲区:AutoCAD Mechanical模块采购量超实际需求2.5倍,仅因工程师惯性选择
2. 成本裂变的传导链条
- 直接浪费:某重工企业因跨基地许可证无法共享,重复采购成本达480万元/年
- 隐性损失:设计任务排队导致的研发周期延长,间接成本可达直接采购费用的3倍
- 合规风险:突击审计发现的越权使用行为,可能引发单次罚金超采购预算15%
3. 管理失效的循环困局
- 数据孤岛:采购、IT、财务三部门需求数据偏差率超55%
- 响应迟滞:传统人工调度模式需3-5天完成许可证调配,无法满足敏捷研发需求
- 价值湮灭:40%的电气设计模块许可证从未被激活,却持续产生维护费用
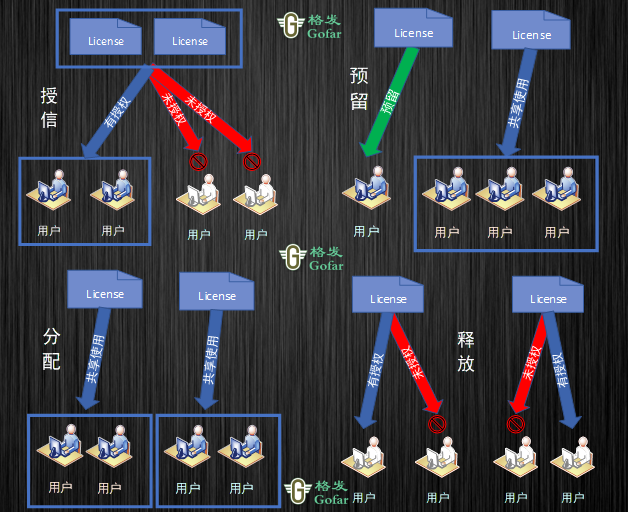
【三维度构建需求分析模型】
一、需求量化引擎(Demand Quantification Engine)
- 行为特征画像
- 通过API抓取工程师操作日志,建立“功能模块-使用时长-操作频率”三维矩阵
- 应用聚类算法识别用户类型(如机械设计重度用户、电气设计边缘用户)
- 构建动态权重模型,区分核心需求(如参数化设计)与临时需求(如图纸批注)
- 项目需求预测
- 基于PLM系统数据,关联BOM清单与设计软件模块依赖关系
- 开发蒙特卡洛模拟算法,预测不同研发阶段许可证需求波动区间
- 建立弹性系数模型(如船体结构设计阶段资源需求弹性系数=2.3)
二、资源调度中枢(Resource Orchestration Hub)
- 智能分配策略
- 设计“三级优先级”调度规则:▶ 关键路径任务(如整车数模发布)享有实时抢占式资源分配▶ 常规任务采用时间片轮转机制▶ 低优先级任务进入队列等待池
- 开发跨地域资源平衡算法,消除生产基地间的“许可证时差”
- 闲置资源回收
- 设置动态心跳检测机制,自动回收超30分钟无响应的会话
- 构建部门资源使用效能排行榜,触发“末位回收再分配”机制
- 建立资源借贷市场模型,允许部门间按项目周期临时交易许可证
三、成本优化决策树(Cost Optimization Decision Tree)
- 采购策略仿真
- 开发TCO(总拥有成本)对比模型,量化永久许可、订阅制、混合模式的成本拐点
- 建立模块采购四象限分析:▶ 高频高价值模块(如3D建模)采用永久许可▶ 低频高价值模块(如CFD集成)采用按需订阅▶ 高频低价值模块(如基础绘图)推动标准化▶ 低频低价值模块(如特定渲染插件)实施淘汰
- 风险对冲机制
- 设置应急资源池(占总资源的10%-15%),应对突发设计变更
- 开发合规性预检系统,自动阻断非授权模块调用
- 建立供应商谈判数据模型,基于历史使用数据争取批量折扣
【实施路径与价值锚点】
阶段化部署路线
- 数据筑基(1-3个周):
- 部署轻量化采集代理,完成全量用户行为数据埋点
- 建立需求基线模型,输出首版《模块使用价值白皮书》
- 动态调优(4-6个周):
- 上线智能调度引擎,实现许可证分配响应时间≤15分钟
- 构建部门级资源使用效能看板
- 战略协同(7-12个周):
- 打通与ERP、PLM系统的数据管道,实现“研发计划-资源需求-采购预算”联动
- 建立AI驱动的采购建议系统,自动生成三年滚动采购规划
量化收益模型
- 成本节约:许可证利用率从58%提升至85%,年均采购预算缩减18%-25%
- 效率提升:设计任务等待时间减少72%,研发周期压缩15%-20%
- 风险控制:100%阻断非合规使用,规避年均2%-3%的潜在罚金
某新能源汽车企业实践显示,部署需求分析模型后,车身设计部门在高峰期获取的许可证数量提升2.8倍,而年度采购费用反而下降12%。更深远的影响在于,通过分析模块使用数据,发现工程师过度依赖传统二维绘图工具,进而推动设计范式向三维参数化转型——这不仅释放了30%的冗余许可证,更使研发效率获得质的飞跃。当每一份软件采购预算都能转化为确定性的研发产出,制造业的数字化转型才真正步入价值创造的深水区。